Transport Safety
Safety Management Regulations
General motor truck (freight) transportation business operators of a certain size are required to establish safety management regulations and notify the Minister of Land, Infrastructure, Transport and Tourism. Yamato Group operating companies subject to this rule have also established safety management regulations in accordance with the law.
The 14 items to be listed in these safety management regulations are: Commitments of Top Management, Responsibilities of Top Management, Safety Policies, etc., Safety Supervisors, Responsibilities and Authority of Personnel, Ensuring Communication and Transmission of Information, Reporting Information on Accidents, etc., Responding to Serious Accidents, Ensuring Compliance with Relevant Laws and Regulations, etc., Education and Training Necessary to Maintain a Safety Management System, Internal Audits, Reviews and Continuous Improvement, Creation and Management of Documents, and Creation and Maintenance of Records.
The Yamato Group also emphasizes the concept of "conducting safety management systematically and continuously through the leadership of top management" as indicated by the law, and is engaged in various efforts to achieve this.
Safety management regulations and transportation safety management at Group companies (published online) *Japanese only
Promotion Structure
Each Group company has established its own safety management system, in accordance with the safety management regulations.
In order to enhance the effectiveness of transportation safety management, we have established a system that allows organizational management through coordination between management departments and transportation personnel in the field, under the leadership of top management. Each Group company engaged in transportation safety management conducts regular reviews by top management, reviews actual performance and results, clarifies problems and issues, and improves upon them.
We have also established a system for sharing important information-such as details of serious transportation accidents-with Yamato Transport corporate headquarters, which oversees and promotes transportation safety throughout the Yamato Group.
Yamato Transport: Head Safety Instructor System
The foundation of Yamato Transport's safety strategy is the head safety instructor system, which has consistently underpinned our safety since its introduction in 1974.
The head safety instructor is a specialist in safety measures, assigned to each major branch. As of March 31, 2023, there are 358 head safety instructors nationwide. Head safety instructors patrol the sales offices under their supervision daily, working to ensure compliance with laws and regulations, improve the driving skills of individual drivers, and thoroughly work to prevent traffic accidents and other industrial accidents.
Other operating companies aside from Yamato Transport have also established head safety instructor systems and other similar systems. For details of numbers at each company, please see our ESG data.
Education on Traffic Safety
Yamato Group companies are working to improve their employees' safety awareness through regular safety education.
Yamato Transport: Internal License System
Yamato Transport drivers hired through rigorous aptitude tests receive training over the course of around one month after joining the company, and can only begin to engage in actual driving duties after obtaining their internal license. Drivers continue to refine their safe driving skills through further training one year after joining the company, regular escort guidance and road patrols by head safety instructors and managers, and driving aptitude checks conducted once every three years.
Yamato Transport: Dash Cam Video Guidance and Escort Guidance
At Yamato Transport's main branches nationwide, safety guidance supervisors and managers provide direct safety guidance to individual drivers through dash cam video guidance and escort guidance.
- 1Dash Cam Video Guidance
Drivers gain necessary advice by watching dash cam videos, recorded while they were driving, together with safety experts and managers. This encourages behavior modification through acquisition of new awareness that enables them to become safer drivers.
- 2Escort Guidance
Escorts accompany and observe drivers during collection and delivery, and check and instruct them in detail as to whether or not they are implementing safe and economical driving.
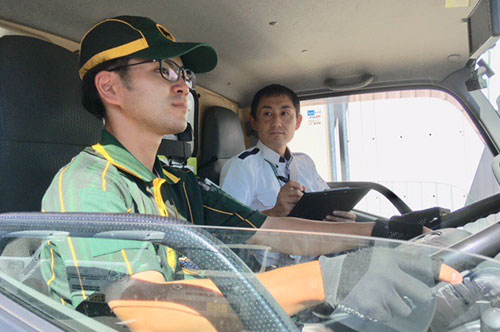
Yamato Transport: Creating Educational Tools
Yamato Transport uses a variety of tools to raise awareness of safety and implement its "safety first" philosophy. These include the information magazine Safety First that shares safety information, a Driver Safety Notebook carried by all drivers, and a "Safety Calendar" that can increase sensitivity to danger through hazard perception training.
We are also working to prevent accidents through a biannual initiative to achieve zero traffic accidents, using actual footage from drive recorders installed in delivery vehicles to compile a collection of "near miss" cases and create traffic safety training videos.
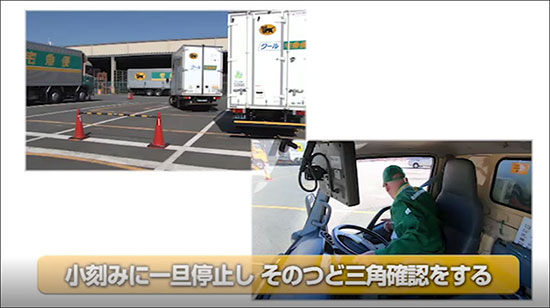
Driver Training Results
Training program | Number of participants in FY2022 (persons) |
---|---|
Escort guidance | 33,688 |
Guidance using drive recorder video | 61,033 |
Yamato Multi Charter: E-Learning
Yamato Multi Charter has introduced an e-learning program entitled "Anzen-Drive: Learn Safe Driving for Peace of Mind." By learning about the following two topics every month, employees are encouraged to improve their safety awareness.
Study Topics
- Guidelines for general guidance and supervision of Ministry of Land, Infrastructure, Transport and Tourism Notification No. 1366* (12 items)
- Preventing serious accidents
*Guidelines for guidance and supervision of drivers of commercial vehicles provided by motor truck (freight) transportation business operators
Safety Management Measures
In order to ensure transportation safety, we have taken various safety management measures, both across the Group and at each Group company individually, in line with our transportation safety management policies.
Yamato Group: Zero Traffic Accident Movement
The Yamato Group conducts a group-wide Zero Traffic Accident Movement in the spring and autumn of each year, which includes overseas operating companies. Yamato Transport has been engaged in the movement since 1970.
A priority issue for the whole Group under the Zero Traffic Accident Movement is to prevent traffic accidents during driving as part of business operations. Operating companies that own vehicles have set their own themes for the movement according to the content of their specific business operations, and are engaged in initiatives to implement these priority items.
Group companies that do not have their own vehicles have also formulated their own safety measures, with priority items such as "prevention of industrial accidents" and "prevention of traffic accidents incurred by employees."
During the movement period, we summarize the state of occurrence of accidents every day for the Group as a whole, and share the current situation with Group members for a certain period. After the end of the period, we ask operating companies where accidents occurred to investigate the causes and consider measures to prevent future recurrences. In this way, we are working to raise safety awareness throughout the entire Group throughout the year.
Yamato Group Companies: Accident-Free Commendation
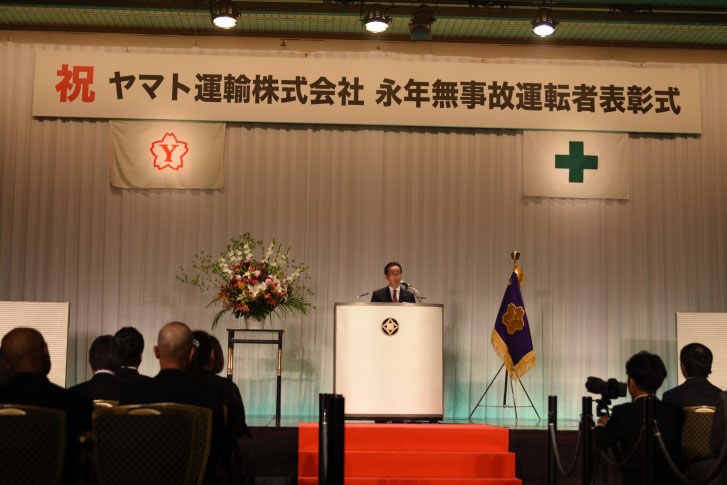
The implementation of Yamato Group's Safety First philosophy is underpinned by the safe driving of its drivers on a daily basis. Every year, Yamato Transport, Okinawa Yamato Transport, Yamato Multi Charter, and Yamato Box Charter commend and reward drivers who excel in safe driving and continue to have no accidents.
Yamato Transport also commended 2,511 locations that achieved zero accidents or disasters for a one-year period as Safety Excellence Offices. (FY2022)
Numbers of accident-free drivers at each company
Yamato Group: G Mark Certification (Motor Truck Transportation Business Operator Safety Assessment Project)
G Mark (Motor Truck Transportation Business Operator Safety Assessment Project) is a certification system operated by the Ministry of Land, Infrastructure, Transport and Tourism (MLIT) which certifies business locations that achieve safety excellence. The program certifies business establishments that work actively to ensure transportation safety, from the viewpoint of making it easier for users to choose businesses that maintain high standards of safety. The Japan Trucking Association-a government-designated organization for the establishing order in the motor vehicle (freight) transportation industry-has set 38 assessment criteria, based on which business operators are certified by the organization's safety evaluation committee.
The Yamato Group is actively acquiring G Mark certification to improve transportation safety.
For details of G Mark certification status at each company, please see our ESG data.
Yamato Transport: Internal Driver Contest (National Safety Competition)
With the aim of improving the driving safety of its professional drivers, maintaining Companywide safety awareness, and improving driving techniques, Yamato Transport has been holding the Yamato Transport Nationwide Safety Meet since 2012. In 2023, four years after the meet was last held, 36 drivers were chosen from over 60,000 across five Yamato Group companies to compete over safe driving skills and knowledge.
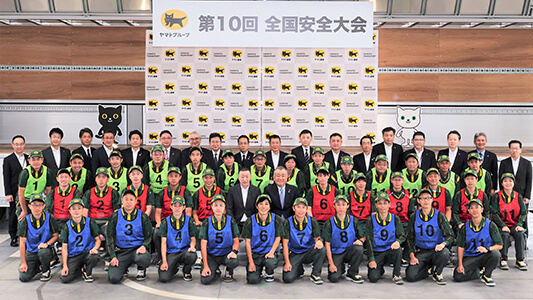
Yamato Transport Co., Ltd.: Development of Head Safety Instructors
Yamato Transport provides leadership training to head safety instructors and specialist head safety instructors are certified twice a year. Step 1 (laws and regulations), Step 2 (driving skills), Step 3 (observation skills), and Step 4 (leadership) certification tests are held, and it is determined whether the head safety instructors have the necessary skills.
Certification step | Number of people certified in FY2022 (persons) |
---|---|
Step 1 (laws and regulations) | 305 |
Step 2 (driving skills) | 286 |
Step 3 (observation skills) | 284 |
Step 4 (leadership) | 190 |
Yamato Transport Co., Ltd.: In-car Terminals Equipped with Communication Functionality Integrating Drive Recorders and Digital Tachographs
Yamato Transport has installed integrated terminal devices in all pickup and delivery vehicles to collect driving data, such as footage collected from drive recorders and driving routes created using information obtained from GPS antennas, in addition to the speed and parking position information already collected by digital tachographs. The data collected by these devices is automatically sent via communications network connections and stored in a cloud-type database in real time. We have also enabled automation in registering "near miss" locations, labor saving for drive start and endpoint settings, and automation of software updates for in-car devices, so that sales drivers can concentrate more on safe driving.
Visualizing and analyzing the driving data collected and centrally managed via these in-car devices, it is possible for head safety instructors and other relevant personnel to more accurately grasp specific details of the driving characteristics of each sales driver. As a result of this, we will be able to provide more finely tuned preventive safe driving training tailored to the individual driving characteristics of each driver.
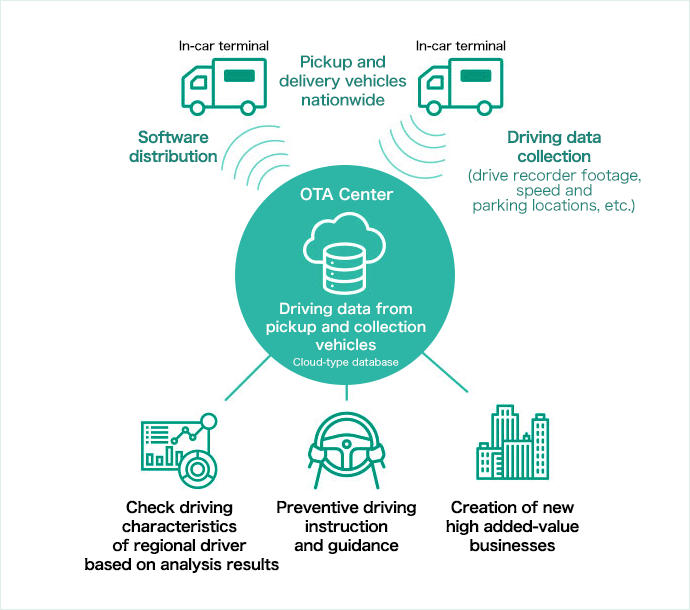
Yamato Autoworks: Thorough Vehicle Maintenance and Management to Support Safety
Yamato Autoworks covers over 3,700 Yamato Group collection and delivery locations, and is responsible for the inspection and maintenance of around 46,000 vehicles. The company has 72 maintenance plants located around Japan, 30 of which are Super Works locations: state-of-the-art factories that pursue greater efficiency of vehicle maintenance systems, consideration for the environment, and ease of work for employees.
Most of these maintenance plants-including Super Works locations-are open 24 hours a day, 365 days a year, and perform statutory periodic inspections on all vehicles by centralized management throughout the year, in addition to rapid response in the event of breakdowns. By continuously checking the status of vehicles and accumulating information, the company also achieves preventive maintenance, performing maintenance on vehicles before breakdowns occur. Of the approximately 930 mechanics, around 700 are qualified automobile inspectors who can perform completion inspections after maintenance work has been completed to ensure that vehicles comply with safety standards. In maintenance, the accuracy of inspections is improved through double-checking conducted by another mechanic, for both midway and completion inspections.
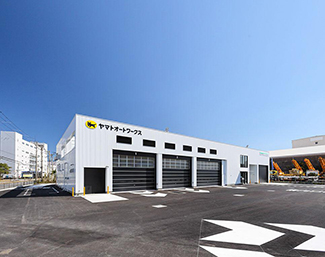